industrial equipment
- Listed: 3 October 2024 3h01
- Expires: 360 days, 15 hours
Description
The latest technologies in predictive maintenance
Predictive maintenance, a constantly evolving field, increasingly relies on cutting-edge technologies to optimize equipment availability and reduce maintenance costs. Here is an overview of the latest trends:
1. Artificial Intelligence and Machine Learning
Deep learning: Artificial neural networks can analyze complex data, such as vibrations, temperatures or electrical currents, to detect subtle anomalies and predict failures with increased accuracy.
Machine learning algorithms: Sophisticated statistical models can identify correlations between different variables and build robust predictive models.
2. Internet of Things (IoT)
Smart sensors: Connected sensors can continuously collect data on the condition of equipment, providing real-time visibility into its operation.
IoT platforms: These platforms centralize and analyze data from multiple sensors, facilitating the implementation of large-scale predictive maintenance solutions.
3. Advanced Data Analytics
Big Data: Processing large amounts of data helps identify long-term trends and detect rare anomalies.
Predictive Analytics: Statistical and machine learning techniques are used to create predictive models that can anticipate failures.
4. Augmented Reality and Digital Twins
Augmented Reality: Augmented reality allows technicians to access contextual information about equipment during maintenance interventions, facilitating problem diagnosis and resolution.
Digital Twins: Creating virtual models of equipment allows simulating different failure scenarios and optimizing maintenance strategies.
5. Blockchain
Traceability: Blockchain ensures data integrity and traceability, increasing trust in the information used for predictive maintenance.
Security: Blockchain offers a high level of security to protect sensitive data.
Concrete Applications
Manufacturing Industry: Prediction of failures on machine tools, optimization of maintenance plans.
Energy: Monitoring wind turbines, optimizing energy production.
Transportation: Predicting vehicle failures, optimizing maintenance operations.
Building: Monitoring heating, ventilation and air conditioning (HVAC) systems, optimizing energy consumption.
In summary, the latest technologies offer considerable opportunities to improve the efficiency and reliability of maintenance operations. By combining artificial intelligence, IoT, data analytics and other emerging technologies, companies can reduce maintenance costs, increase equipment availability and improve customer satisfaction.
The integration of artificial intelligence into industrial processes: a revolution in progress
Artificial intelligence (AI) is transforming the industrial landscape. By empowering machines with cognitive capabilities, it is ushering in a new era of more efficient, flexible, and intelligent production.
Key benefits of AI in manufacturing include:
Process optimization: AI can analyze vast amounts of data in real time to identify bottlenecks, inefficiencies, and opportunities for improvement. This helps optimize production flows, reduce downtime, and increase productivity.
Improve quality: Using machine learning algorithms, AI can detect manufacturing defects early, ensuring the quality of finished products and reducing costs related to returns and rework.
Predictive maintenance: By analyzing data from sensors installed on equipment, AI can predict failures before they occur, allowing maintenance interventions to be planned proactively and avoiding unexpected production stoppages.
Production customization: AI can customize products to meet the specific needs of each customer, while maintaining competitive production costs.
Enhanced safety: AI can be used to detect safety anomalies in industrial processes and to strengthen the protection of facilities.
Concrete applications of AI in industry:
Quality control: AI is used to inspect finished products and detect visual or dimensional defects.
Collaborative robotics: Collaborative robots equipped with AI can work closely with humans to perform complex and repetitive tasks.
Logistics: AI optimizes warehouse management, transportation planning, and the supply chain.
Predictive maintenance: AI is used to monitor the condition of equipment and predict failures.
Energy optimization: AI can reduce the energy consumption of industrial processes.
Challenges:
Data quality: The quality of the data used to train AI models is crucial. Incomplete, erroneous or biased data can lead to inaccurate results.
Security: Protecting sensitive data used by AI systems is a major issue.
Cost: Implementing AI solutions can represent a significant investment.
Skills: Developing and implementing AI solutions requires specific skills that can be difficult to find.
The integration of artificial intelligence into industrial processes is a revolution in progress that will profoundly transform production methods. By leveraging the benefits of AI, companies can improve their competitiveness, reduce costs and meet customer expectations more efficiently. However, it is important to address challenges related to data quality, security and skills to fully leverage the potential of this technology.
To go further, you may be interested in these topics:
Deep learning and its application in industry
Artificial neural networks and their role in industrial data analysis
Natural language processing and its applications in predictive maintenance
Computer vision and its use in quality control
Materials of the future for industrial equipment: a revolution in progress
The manufacturing industry is constantly evolving, driven by the growing demand for more efficient, more durable and more environmentally friendly products. Materials play a crucial role in this transformation. The materials of the future, thanks to their exceptional properties, open up new perspectives for industrial equipment.
What are the characteristics of the materials of the future?
High performance: The materials of the future must offer superior mechanical, thermal and electrical performances to traditional materials.
Lightness: Reducing the weight of equipment is a major challenge to reduce energy consumption and improve mobility.
Durability: Materials must be resistant to corrosion, wear and shock, in order to increase the lifespan of equipment.
Recyclability: As the circular economy is a priority, materials must be easily recyclable or biodegradable.
Functionality: The materials of the future will be able to integrate advanced functionalities, such as electrical conductivity, the ability to change color or self-repair.
What are the main materials of the future?
Composite materials: These materials combine the properties of several materials (fibers, resins, metals) to obtain specific characteristics. They are used in many sectors, from aeronautics to the automobile industry.
Light metals: Aluminum, magnesium and light alloys are increasingly used to reduce the weight of equipment.
Technical ceramics: Ceramics offer excellent resistance to heat, wear and corrosion. They are used in engines, turbines and cutting tools.
Smart polymers: These polymers can react to external stimuli (temperature, pH, light) by modifying their properties. They find applications in robotics, medicine and technical textiles.
Nanostructured materials: By manipulating matter at the nanoscale, it is possible to create materials with new properties, such as graphene, which is stronger than steel and lighter than aluminum.
What are the industrial applications of these materials?
Aeronautics: Composite materials make it possible to manufacture lighter and more fuel-efficient aircraft.
Automotive: Lightweight materials and composite materials help reduce the mass of vehicles and improve their performance.
Energy: Ceramic materials are used in gas turbines and solar panels.
Biomedicine: Smart polymers are used to manufacture medical implants and diagnostic devices.
Consumer goods: Nanostructured materials are used to create stronger, lighter and more functional products.
Challenges to be met
Cost: The materials of the future are often more expensive to produce than traditional materials.
Implementation: New manufacturing processes must be developed to implement these materials.
Regulations: Regulations must evolve to take into account new materials and their impacts on the environment and health.
In conclusion, the materials of the future will revolutionize industrial equipment by offering unmatched performance. However, many challenges remain for these materials to be widely adopted.
To go further, you can be interested in these subjects:
3D printed materials
Self-repairing materials
Bio-inspired materials
The Latest Safety Standards for Industrial Equipment: An Overview
Safety standards for industrial equipment are constantly evolving to adapt to technological advances and new identified risks. These standards aim to ensure worker safety, prevent accidents and protect the environment.
Why are safety standards important?
Worker protection: Standards significantly reduce the risk of workplace accidents, such as injuries, burns and electrocutions.
Regulatory compliance: Failure to comply with standards can result in significant financial and legal penalties.
Improved productivity: Safe equipment is generally more reliable and less prone to breakdowns, which improves productivity.
Social responsibility: Compliance with safety standards demonstrates the company’s commitment to the safety and well-being of its employees.
The main safety standards for industrial equipment
Safety standards are numerous and vary depending on the type of equipment and the industry. Here are some of the most important standards:
European standards:
IEC 61010: Electrical equipment for measurement, control and laboratory use.
ISO 13849: Safety of machinery – Safety-related functional parts – Part 1: General concepts for system design.
ISO 14120: Safety of machinery – Guards – General principles for design and assessment.
American standards:
NFPA 70: National Electrical Code
OSHA: Occupational Safety and Health Administration
Industry-specific standards:
ATEX: Potentially explosive atmospheres (for chemical, petroleum, etc. industries)
FDA: Food and Drug Administration (for the food industry)
Recent developments in safety standards
Integration of new technologies: The standards take into account the rapid evolution of technologies, including automation, robotics and artificial intelligence.
Focus on ergonomics: Standards focus on the ergonomics of workstations to reduce musculoskeletal disorders.
Taking into account emerging risks: Standards evolve according to new identified risks, such as risks related to nanomaterials or cyber security.
How to stay informed about the latest standards?
To stay informed about the latest safety standards, it is recommended to:
Consult standardization organizations: Organizations such as AFNOR, ISO and IEC regularly publish new standards and updates.
Subscribe to specialized journals: Many journals deal with industrial safety issues and provide information on the latest regulations.
Participate in training: Training provides the knowledge needed to implement safety standards within the company.
In conclusion, safety standards play an essential role in protecting workers and preventing accidents. It is important for companies to stay up to date with the latest developments and implement the necessary measures to ensure the compliance of their equipment.
To go further, you can learn about the following topics:
Risk assessment: How to identify and assess the risks associated with the use of industrial equipment.
Worker training: The importance of training workers in safety rules.
Preventive maintenance: How preventive maintenance contributes to equipment safety.
Preventing accidents at work in the industrial sector: a major challenge
Preventing workplace accidents in the industrial sector is a key issue for the health and safety of workers, but also for the sustainability of companies. Many regulations and standards have been put in place to regulate industrial activities and reduce risks.
The main risks in industry
Industrial risks are multiple and can vary depending on the sector of activity. Among the most frequent, we find:
Mechanical risks: Trapping, cuts, crushing related to the use of machine tools.
Electrical risks: Electric shocks, electric arcs.
Chemical risks: Exposure to dangerous products, inhalations, projections.
Physical risks: Noise, vibrations, extreme temperatures, radiation.
Risks related to the work environment: Falls from height, slips, trips.
Preventive measures
To prevent these risks, many measures can be implemented:
Assessment of occupational risks: This is the first essential step to identify the dangers present in the company and implement corrective actions.
Worker training: Training is essential to raise employees’ awareness of the risks and teach them first aid.
Personal protective equipment (PPE): PPE must be adapted to each risk and must be worn by workers.
Equipment maintenance: Regular maintenance can detect anomalies and prevent breakdowns that cause accidents.
Workstation layout: Workstation layout must be ergonomic and adapted to the tasks to be performed.
Signage: Clear and visible signage can alert workers to the dangers present.
Emergency procedures: Emergency procedures must be put in place and regularly tested to deal with emergency situations.
Standards and regulations
Many standards and regulations govern the prevention of industrial risks. In France, the Labor Code and ministerial decrees define employers’ obligations in terms of safety. ISO 45001 standards (management of health and safety at work) are also increasingly used.
The benefits of prevention
Preventing workplace accidents has many advantages:
Improving the quality of life at work: A safe working environment promotes employee well-being.
Reducing costs: Work accidents result in significant costs (work stoppages, compensation, etc.). Prevention helps reduce these costs.
Improving the company’s image: A company that implements prevention measures shows its commitment to safety.
In conclusion, preventing workplace accidents is a major issue for all industrial companies. By implementing appropriate measures and complying with the standards in force, it is possible to create a safe and healthy working environment for all.
To go further, you may be interested in:
The different methods of risk analysis (AMDEC, Bow-tie method, etc.)
Collective protective equipment
The most frequent work accidents in industry and their causes
The latest innovations in industrial safety
Legal obligations regarding maintenance and inspection of equipment
Equipment maintenance and inspection are an essential part of preventing occupational risks. Current regulations impose specific obligations on employers in this area, in order to guarantee worker safety and the compliance of installations.
Why is maintenance mandatory?
Worker safety: Regular maintenance makes it possible to detect and repair anomalies that could cause accidents at work.
Regulatory compliance: Legislative and regulatory texts impose maintenance obligations for certain types of equipment.
Equipment reliability: Preventive maintenance increases the lifespan of equipment and optimizes its operation.
Environmental protection: Maintenance can help reduce pollutant emissions and limit the environmental impact of activities.
What are the legal obligations?
Legal obligations regarding maintenance vary depending on the type of equipment, the sector of activity and the country. However, the following obligations are generally found:
Establish and maintain a maintenance plan: This plan must define the maintenance operations to be carried out, their frequency and the persons responsible.
Perform regular inspections: Inspections are used to check the operating condition of the equipment and detect anomalies.
Keep a maintenance log: This log must record all maintenance operations carried out.
Train staff: Maintenance personnel must be trained and competent to carry out the operations.
The French Labor Code, for example, requires employers to maintain work equipment in compliance with legal and regulatory requirements.
What equipment is concerned?
Maintenance obligations concern a wide range of equipment, including:
Lifting equipment: overhead cranes, hoists, forklifts, etc.
Electrical installations: electrical panels, machine tools, etc.
Pressure equipment: boilers, tanks, etc.
Measuring devices: scales, meters, etc.
Collective protection equipment: safety devices, barriers, etc.
The consequences of a lack of maintenance
Failure to comply with legal maintenance obligations can have serious consequences:
Workplace accidents: Accidents can have dramatic consequences for workers and those around them.
Production stoppages: A breakdown due to a lack of maintenance can lead to significant production losses.
Criminal and administrative sanctions: Employers can be prosecuted in the event of a workplace accident linked to a lack of maintenance.
Civil liability: The employer can be held liable for damage caused by defective equipment.
In conclusion, equipment maintenance is a legal obligation that contributes to worker safety, the sustainability of installations and regulatory compliance. It is therefore essential to set up a rigorous maintenance system adapted to each company.
For more information, do not hesitate to consult the legislative and regulatory texts in force in your country, as well as the recommendations of occupational risk prevention organizations.
Keywords: maintenance, inspection, equipment, safety, regulation, Labor Code, risk prevention
Would you like to learn more about a particular aspect of equipment maintenance? For example, you can ask me questions about the standards applicable to a specific type of equipment, preventive maintenance methods or the consequences of an accident linked to a lack of maintenance.
Improving the energy efficiency of industrial equipment: a major challenge
Improving the energy efficiency of industrial equipment is a major challenge for companies, both for economic reasons (reducing energy costs) and environmental reasons (reducing greenhouse gas emissions). Here are some ways to optimize the energy consumption of your equipment:
1. Energy audit:
Identify the most energy-intensive items: An energy audit allows you to locate the equipment that consumes the most energy and identify sources of losses.
Assess the potential for improvement: The audit quantifies the energy savings that can be achieved through energy efficiency measures.
2. Choice of equipment:
Prioritize energy-efficient equipment: When replacing equipment, opt for labeled models (for example, A+++ for electric motors).
Consider the complete life cycle: Assess not only energy consumption during operation, but also the environmental impacts related to manufacturing and recycling.
3. Process optimization:
Fine parameter adjustment: Adjust equipment parameters (pressure, temperature, flow rate) to optimize their operation.
Preventive maintenance: Regular maintenance keeps equipment in good condition and avoids energy losses due to breakdowns or premature wear.
4. Innovative technologies:
Variable speed motorization: Adapt motor speed to the actual load to reduce energy consumption.
Energy recovery systems: Recover energy lost in the form of heat (e.g. for heating) or cold (for air conditioning).
Intelligent control and monitoring: Implement intelligent control and monitoring systems to optimize energy consumption based on actual needs.
5. Employee awareness:
Training: Train employees in good energy-saving practices.
Communication: Implement communication actions to raise employee awareness of the importance of energy efficiency.
6. Other measures:
Thermal insulation: Reduce heat loss by insulating buildings and equipment.
LED lighting: Replace old lighting sources with LEDs, which consume much less energy.
Compressed air management: Optimize the production and distribution of compressed air to reduce leaks and energy losses.
The benefits of energy efficiency
Reducing energy costs: Savings on energy bills can be significant.
Reducing carbon footprint: Reducing energy consumption helps combat climate change.
Improving brand image: A company committed to energy efficiency strengthens its image.
Regulatory compliance: More and more regulations impose energy efficiency targets.
In conclusion, improving the energy efficiency of industrial equipment is a complex process that requires a comprehensive approach. By combining different measures, companies can achieve significant energy savings and contribute to a more sustainable future.
To go further, do not hesitate to consult the following resources:
ADEME: Environment and Energy Management Agency
Ministry of Ecological Transition
Specialized energy efficiency design offices
Strategies to reduce production costs through equipment modernization
Industrial equipment modernization is a powerful lever to optimize production processes and reduce costs. By investing in more efficient and effective technologies, companies can gain competitiveness and improve profitability.
Here are some key strategies to reduce production costs through equipment modernization:
1. Process automation
Robotization: Replacing manual tasks with robots increases productivity, reduces human error, and improves product quality.
Automated control systems: Automating control processes optimizes production, reduces downtime, and improves accuracy.
2. Energy optimization
Energy-efficient equipment: Choosing more energy-efficient equipment can reduce energy consumption costs.
Smart energy management: Implementing energy management systems optimizes consumption based on demand.
3. Predictive maintenance
IoT sensors: The use of connected sensors allows monitoring the status of equipment in real time and detecting anomalies before they cause breakdowns.
Data analysis: The analysis of data collected by sensors allows maintenance to be planned and downtime to be reduced.
4. Production flexibility
Versatile machines: Versatile machines allow rapid adaptation to production changes and reduce series changeover times.
Modular production: Modular production facilitates product customization and reduces storage costs.
5. Waste reduction
Process optimization: Optimizing production processes reduces raw material losses and waste.
Recycling: Implementing recycling systems allows waste to be recovered and disposal costs to be reduced.
6. Quality improvement
Automated quality control: Automating quality controls allows defects to be detected more quickly and product quality to be improved.
Reduction of scrap: Better product quality leads to a reduction in scrap and associated costs.
The benefits of modernization
Reduction of production costs: Decrease in energy, labor, maintenance and scrap costs.
Improvement of productivity: Increase in production rate and reduction of downtime.
Improvement of product quality: Reduction of defects and compliance with standards.
Increased flexibility: Ability to adapt quickly to market changes.
Social and environmental responsibility: Reduction of the environmental footprint and improvement of working conditions.
In conclusion, the modernization of industrial equipment is a strategic investment that improves the competitiveness of companies and adapts to the challenges of the energy and digital transition. By combining these different strategies, companies can optimize their production processes and significantly reduce their costs.
To go further, you may be interested in:
Industry 4.0: This industrial revolution is based on the digitalization and interconnection of equipment.
Grants and financial aid: Many systems exist to support companies in their modernization projects.
Case studies: The analysis of concrete cases allows us to better understand the benefits of modernization.
The importance of preventive maintenance to extend equipment life
Preventive maintenance is a strategic approach that aims to anticipate breakdowns and ensure the proper functioning of industrial equipment. By carrying out regular inspections and scheduled interventions, companies can significantly extend the life of their facilities and reduce the costs associated with unplanned repairs.
Why is preventive maintenance essential?
Reduction of unexpected breakdowns: By detecting potential problems before they become breakdowns, preventive maintenance limits production downtime and productivity losses.
Extension of equipment life: By carrying out regular maintenance, the natural wear and tear of equipment is slowed down and its performance is optimized.
Improvement of safety: Preventive maintenance makes it possible to identify potential risks and implement the necessary corrective measures to ensure worker safety.
Cost optimization: Although preventive maintenance requires an initial investment, it can save money in the long term by avoiding significant repair costs and production losses.
The Benefits of Preventive Maintenance
Increased Equipment Reliability: Regular maintenance improves equipment reliability and reduces the risk of failure.
Better Product Quality: Well-maintained equipment produces higher quality products, reducing scrap costs.
Optimized Energy Consumption: Preventive maintenance helps detect energy inefficiencies and implement corrective measures.
Improved Productivity: By reducing downtime, preventive maintenance helps increase overall productivity.
The Principles of Preventive Maintenance
Planning: Establish a precise maintenance plan, defining the tasks to be performed, the frequency of interventions and the resources required.
Regular Inspection: Perform visual and functional inspections of equipment at regular intervals.
Lubrication: Perform lubrication operations according to the manufacturer’s recommendations.
Replacement of Worn Parts: Replace worn or defective parts before they cause a breakdown.
Cleaning: Keep equipment clean to prevent the accumulation of dirt and dust.
Preventive maintenance tools
CMMS (Computerized Maintenance Management System): CMMS software allows you to centrally manage all maintenance-related information.
IoT sensors: Connected sensors allow you to monitor the condition of equipment in real time and detect anomalies.
Vibration analysis: This technique allows you to detect mechanical defects before they cause significant damage.
Thermography: Thermography can detect overheating and insulation defects.
In conclusion, preventive maintenance is an essential investment for any company wishing to optimize the performance of its equipment, reduce costs and guarantee the safety of its employees. By adopting a proactive approach to maintenance, companies can extend the life of their facilities and improve their competitiveness.
To go further, you may be interested in:
The different types of maintenance: preventive, corrective, conditional
Maintenance key performance indicators (KPIs)
Maintenance standards and regulations
Choosing the right industrial equipment is a strategic decision that can have a significant impact on productivity, product quality and the profitability of a company. Here are some tips to help you make the right choice:
1. Define your needs precisely
What is the objective? Improve productivity, reduce costs, improve quality?
What are the tasks to be accomplished? What are the operations that the equipment must perform?
What is the production volume? What is the required production capacity?
What are the environmental constraints? Are there specific regulations to comply with?
2. Evaluate the different options
Compare technical characteristics: Power, precision, dimensions, etc.
Evaluate reliability and durability: Look for equipment known for its robustness.
Compare costs: Consider the acquisition cost, maintenance costs and energy costs.
Consider additional features: Certain features can increase productivity or facilitate use.
3. Consider the working environment
Available space: Check that the equipment fits into the production space.
Working conditions: Temperature, humidity, vibrations, etc.
Compatibility with existing equipment: Ensure good integration into the existing production system.
4. Consult the experts
Suppliers: Suppliers can advise you on the equipment best suited to your needs.
Manufacturers: Manufacturers can provide you with detailed technical information on their products.
Engineering advice: An engineer can help you carry out a feasibility study and choose the most suitable solution.
5. Consider the following selection criteria:
Safety: The equipment must comply with current safety standards.
Ease of use: Equipment that is easy to use reduces errors and increases productivity.
Maintenance: Equipment that is easy to maintain reduces maintenance costs.
Modularity: Modular equipment can adapt to your changing needs.
Total cost of ownership: Do not limit yourself to the purchase price, but take into account all costs over the life of the equipment.
6. Do not neglect training
Once the equipment has been chosen, it is essential to train personnel in its use to optimize its performance and ensure safety.
In summary, the choice of industrial equipment is an important decision that must be made with full knowledge of the facts. By following these tips, you will be able to select the equipment best suited to your needs and your budget.
A few additional questions to refine your choice:
What is your budget?
What are the environmental standards to be respected?
What is the desired lifespan of the equipment?
Do you need local after-sales service?
Eco-responsible industrial equipment: a major challenge
Industry, long associated with intensive energy consumption and significant environmental impacts, is increasingly turning to more sustainable solutions. Eco-responsible industrial equipment is at the heart of this transition.
What is eco-responsible industrial equipment?
It is equipment designed and manufactured with respect for the environment in mind, minimizing its impact throughout its life cycle: from production to disposal.
The criteria for eco-responsible equipment:
Eco-friendly materials: Use of recycled, bio-sourced materials or materials from sustainably managed forests.
Reduced energy consumption: Optimization of energy consumption thanks to innovative technologies (high-efficiency motors, energy recovery, etc.).
Reduction of emissions: Limiting greenhouse gas and pollutant emissions.
Ease of maintenance and repair: Extension of the equipment’s lifespan and reduction of waste.
Recyclability: Ease of recycling or recovery at the end of its life.
The advantages of eco-responsible equipment:
Cost reduction: Reduced energy consumption, maintenance costs and costs related to waste disposal.
Improved brand image: A company that uses eco-responsible equipment conveys a positive image to its customers and stakeholders.
Regulatory compliance: Compliance with current environmental standards.
Contribution to the energy transition: Reduction of the company’s carbon footprint.
Examples of eco-responsible industrial equipment:
Low-energy machine tools: equipped with high-efficiency motors and energy recovery systems.
Energy-efficient heating and air conditioning systems: heat pumps, geothermal energy, etc.
Industrial LED lighting: offering a longer lifespan and reduced energy consumption.
Collaborative robots: designed to work closely with humans, thus optimizing production processes.
Wastewater treatment systems: to recycle water and reduce pollutant discharges.
How to choose eco-responsible industrial equipment?
Find out about environmental labels: Look for equipment certified by recognized organizations.
Compare technical data sheets: Analyze energy performance, materials used and recycling conditions.
Favor suppliers committed to a sustainable development approach.
Call on an energy efficiency expert.
In conclusion, eco-responsible industrial equipment offers many advantages both environmentally and economically. By investing in these technologies, companies contribute to a more sustainable future while strengthening their competitiveness.
To go further, do not hesitate to consult the following resources:
ADEME: Environment and Energy Management Agency
Ministry of Ecological Transition
Manufacturers of eco-responsible industrial equipment
Industrial robots: essential tools for modern production
Industrial robots have revolutionized the manufacturing sector by automating many repetitive and dangerous tasks. They offer unmatched flexibility, precision and endurance, thus optimizing production processes and improving product quality.
How an industrial robot works
An industrial robot is a programmable, multifunctional manipulator with numerical control. It is composed of several elements:
The mechanical structure: It defines the range and mobility of the robot.
The actuators: They allow the different elements of the structure to be moved.
The control system: It manages the robot’s movements according to the programs.
The effectors: They are located at the end of the robot’s arm and allow specific tasks to be performed (gripper, welding torch, etc.).
Applications of industrial robots
The applications of industrial robots are very varied and cover many sectors of activity:
Automotive: Welding, painting, assembly, handling of heavy parts.
Electronics: Assembly of electronic components, testing, packaging.
Food industry: Packaging, palletizing, handling fragile products.
Medical: Manufacturing of medical devices, surgical assistance.
Aeronautics: Assembly of complex parts, painting.
Advantages of using industrial robots
Increased productivity: Robots work without interruption and at a constant speed, which allows for an increase in production volume.
Improved quality: Robots perform tasks with great precision, reducing errors and scrap.
Flexibility: Robots can be easily reprogrammed to adapt to new tasks or production changes.
Safety: Robots can perform dangerous or repetitive tasks, reducing the risk of workplace accidents.
Cost reduction: Robots help reduce long-term production costs through improved efficiency and reduced labor costs.
The different types of industrial robots
Cartesian robots: They move along three perpendicular axes.
Cylindrical robots: They move around a central axis and along a vertical axis.
Spherical robots: They move in a spherical area.
SCARA robots: They are specially designed for assembly applications.
Articulated robots: They offer great flexibility of movement thanks to several joints.
The challenges of implementing industrial robots
Investment cost: The acquisition and implementation of an industrial robot represents a significant investment.
Staff training: It is necessary to train staff in programming and maintaining robots.
Flexibility: Robots can be less flexible than humans for certain complex or unforeseen tasks.
In conclusion, industrial robots have become indispensable tools in many industrial sectors. They offer many advantages in terms of productivity, quality and safety. However, their implementation requires careful consideration and consideration of the issues related to investment, training and flexibility.
To go further, you may be interested in:
Collaborative robotics: Robots designed to work closely with humans.
Artificial intelligence: The integration of AI into robots to allow them to learn and adapt.
Safety standards: The standards to be respected to guarantee the safety of workers in a robotic environment.
Spare parts inventory management: a strategic issue for industry
Effective spare parts inventory management is a key element to ensure the continuity of production and the availability of industrial equipment. Poor management can lead to costly production downtime, reduced customer satisfaction and increased maintenance costs.
The challenges of spare parts inventory management
Minimize costs: Too much inventory leads to high storage costs, while too little inventory can lead to production downtime.
Optimize parts availability: It is essential to have the necessary parts at the right time to carry out repairs and maintenance.
Improve responsiveness: Effective inventory management reduces intervention times and responds quickly to customer needs.
Prevent obsolescence: It is important to manage inventory according to the life cycle of the equipment and to plan for replacements.
The challenges of spare parts inventory management
The diversity of parts: Industrial companies often use a large number of different spare parts, which complicates inventory management.
Demand variability: The demand for spare parts can be difficult to predict, especially for older equipment.
Storage constraints: Spare parts must be stored in suitable conditions to preserve their quality.
Logistics costs: Inventory management involves transport, storage and handling costs.
Solutions for optimizing spare parts inventory management
ABC classification: This method is used to classify parts into three categories (A, B, C) based on their value and importance. Class A parts, the most important, require more rigorous management.
The economic order quantity (EOQ) method: This method is used to determine the optimal quantity to order to minimize storage and ordering costs.
Computerized maintenance management software (CMMS): This software is used to monitor the condition of equipment, plan maintenance and manage spare parts inventories.
Predictive maintenance: By anticipating breakdowns, predictive maintenance reduces the need for spare parts and optimizes inventories.
Collaboration with suppliers: A good relationship with suppliers allows you to benefit from shorter delivery times and advantageous payment terms.
The benefits of good spare parts inventory management
Cost reduction: Optimization of storage costs, reduction of repair costs and improvement of productivity.
Improvement of customer satisfaction: Reduction of intervention times and availability of parts.
Increase in the lifespan of equipment: Regular preventive maintenance helps to extend the lifespan of equipment.
Improvement of brand image: Effective inventory management is a guarantee of professionalism and reliability.
In conclusion, optimal management of spare parts inventories is essential to guarantee the performance and availability of industrial equipment. By implementing best practices and using the right tools, companies can reduce their costs, improve their productivity and strengthen their competitiveness.
To go further, you may be interested in:
Smart warehouses: Technological solutions to optimize inventory management.
Augmented reality: A technology that can assist technicians during maintenance interventions.
3D printing: A solution for quickly manufacturing spare parts on site.
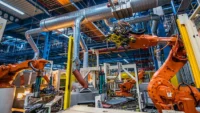
industrial equipment
149 total views, 28 today
Sponsored Links
equipment and supplier manufacturing
Equipment and supplier manufacturing China is a major hub for equipment and supplier manufacturing, offering a wide range of products and services to meet global […]
45 total views, 31 today
where to find additional security verification ?
where to find additional security verification ? Additional security verification, also known as two-factor authentication (2FA) or multi-factor authentication (MFA), is usually found in the […]
123 total views, 0 today
are random security checks really random ?
https://lifehacker.com/why-youre-always-randomly-selected-for-additional-airpo-1840362690https://lifehacker.com/why-youre-always-randomly-selected-for-additional-airpo-1840362690 Why You’re Always ‘Randomly Selected’ For Additional … – Lifehacker Despite TSA claiming the process is random, it isn’t without significant criticism. In 2012, […]
129 total views, 1 today
why information security is important in an organization ?
why information security is important in an organization ? Information security is crucial for organizations of all sizes and across industries. Here’s a breakdown of […]
78 total views, 0 today
when will social security checks be deposited this month ?
https://www.nerdwallet.com/article/investing/social-security/social-security-payment-schedulehttps://www.nerdwallet.com/article/investing/social-security/social-security-payment-schedule Social Security Payment Schedule: November/December 2023 – NerdWallet 30 oct. 2023Nov. 15: If your birthday falls on any day from the 11th to the […]
63 total views, 1 today
when will one punch man end ?
when will one punch man end ? Here are some links that might be useful to you: https://in.ign.com/one-punch-man/173446/news/one-punch-man-manga-to-end-soon-artist-yusuke-murata-clears-the-airhttps://in.ign.com/one-punch-man/173446/news/one-punch-man-manga-to-end-soon-artist-yusuke-murata-clears-the-air One Punch Man Manga to End Soon? […]
90 total views, 2 today
who look after them ?
https://www.merriam-webster.com › thesaurus › look afterhttps://www.merriam-webster.com › thesaurus › look after 68 Synonyms & Antonyms of LOOK AFTER – Merriam-Webster phrase Definition of look after […]
64 total views, 0 today
when should performance management take place ?
https://www.forbes.com › sites › forbesbusinesscouncil › 2021 › 02 › 12 › performance-management-six-best-practices-in-the-new-normalhttps://www.forbes.com › sites › forbesbusinesscouncil › 2021 › 02 › 12 › performance-management-six-best-practices-in-the-new-normal […]
93 total views, 0 today
where are ipad screen recordings saved ?
https://support.apple.com/guide/ipad/take-a-screen-recording-ipaddf78ce08/ipadoshttps://support.apple.com/guide/ipad/take-a-screen-recording-ipaddf78ce08/ipados Take a screen recording on iPad – Apple Support Screen recordings are automatically saved to your photo library in the Photos app . To […]
54 total views, 0 today
what do you think how do you ?
what do you think how do you ? Here are some links that might be useful to you: https://writingtips.org/how-do-you-think-or-what-do-you-thinkhttps://writingtips.org/how-do-you-think-or-what-do-you-think ‘How Do You Think’ or ‘What […]
61 total views, 1 today